Ways to make maintenance effective at a water park
By Chris Biancofiore
It goes without saying that safety, maintenance, and saving money are important at park facilities. But think about how these three concepts connect for a water park to thrive.
Good, consistent maintenance mitigates safety risks that are inherent in creating fun and thrills with water. In more than 20 years in the industry as a manufacturer, I have seen great as well as not-so-great practices when it comes to maintenance. Here is how proper care of equipment will ensure safety AND avoid flushing money down the drain.
THE FOUNDATION
Good Planning As Half The Battle
Exemplary water parks create a maintenance plan and budget annually. The plan is based on recommendations from the original equipment manufacturer (OEM), either from an operation and maintenance (O&M) manual or from an inspection report. Shutdowns are scheduled to perform work in off hours, or during the low season for those parks that operate year-round. Through advanced planning, costs are kept under control.
In contrast, a water park operating without such a plan reacts to maintenance or safety issues as they occur, which inevitably leads to forced shutdowns and costly downtime, one-star reviews, and lost revenue—not to mention large, unexpected expenditures.
Action: Design an operations and maintenance program prior to the start of the season to cover topics such as water quality, signage, dispatch training, water depth and flow rates, surface condition, and environmental protection—all with an overarching focus on safety. Refer to the O&M manuals as well as codes defined by local jurisdiction when creating a program.
Tip: For those facing a staff shortage, consider an OEM-approved third-party to carry some of the load. Also, include the ordering of parts in the plan, as these may require a long lead time and some items may be out of stock before the season begins, when everyone else is looking for the same parts.
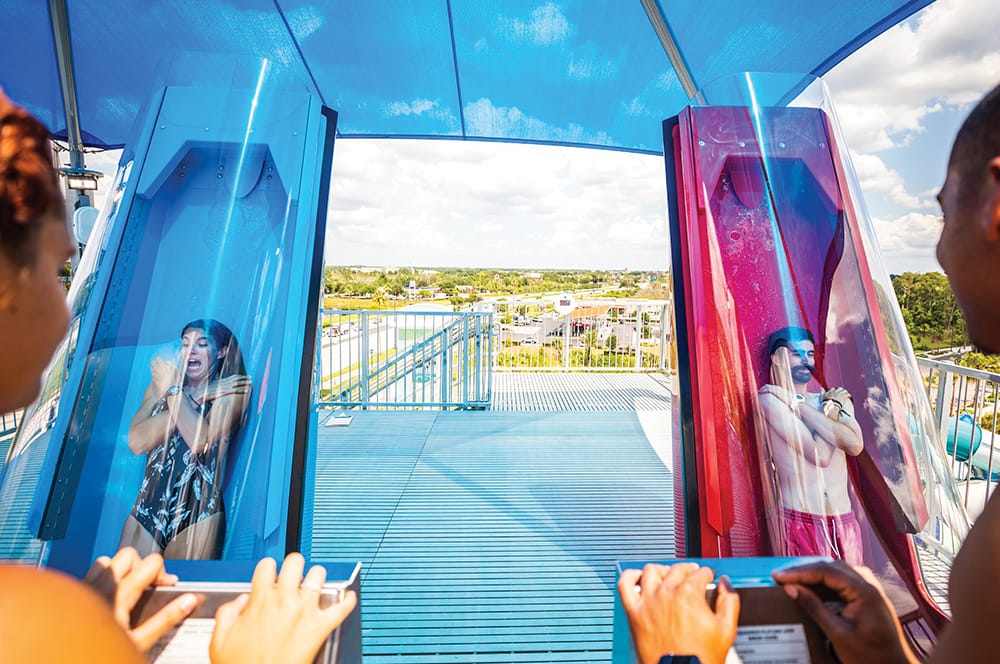
Welcoming Eyes That Scrutinize: Inspections
OEMs know their products best, so diligent water-park employees invite them to inspect the equipment if it’s more than five years old or showing signs of significant wear. After an inspection, these operators will put recommendations from the report into action to keep the equipment in safe, running order.
Don’t wait until an accident or a close call happens before contacting the OEM for an inspection.
Action: If equipment has not been consistently maintained for a few years, schedule an inspection from the original manufacturer. During the season is a great time to do this because the inspector can see the condition of the equipment while it is in operation.
Locating The Operation And Maintenance Manual
Great water-park operators respect the specifications and instructions in the O&M manual. Easily accessible to pertinent staff members, the manual is the first place to look for answers to questions regarding equipment.
Don’t operate off “gut feelings” just because no one happens to know where the O&M manuals are.
Action: If a manual is lost, contact the OEM for a copy. Instill in the team that a smooth operation depends on following this document.
PRODUCTS AND MATERIALS
Fiberglass—The Surface That Makes The Biggest Impression
Looks matter. Water parks that receive good online reviews have slides that look shiny, new, and safe. These operators know the difference between environmental exposure, such as UV and calcium build-up, compared to friction wear, and perform maintenance tasks accordingly.
The opposite is operating water slides with chips and cracks and also faded colors that look unappealing to guests. Allowing small cracks to become big cracks lead to unsafe operations and eventually costly replacement. Another poor practice is irregular cleaning, which results in residue build-up—even small amounts of which can make a slide unsafe to operate.
Action: Check slides daily before turning on the water. Clean, buff, and wax as prescribed in the O&M manual to keep the OEM finish and prevent sunscreen, dirt, minerals, rust, and other deposits from accumulating.
Have a professional inspect water slides every season for fiberglass wear and tear due to friction, UV exposure, and water chemistry. Repair small cracks and chips before they get bigger and eventually cause injuries or damage ride vehicles.
Refill the joints between fiberglass sections to prevent leaks. After all, unnecessary water consumption costs money and does damage to the environment.
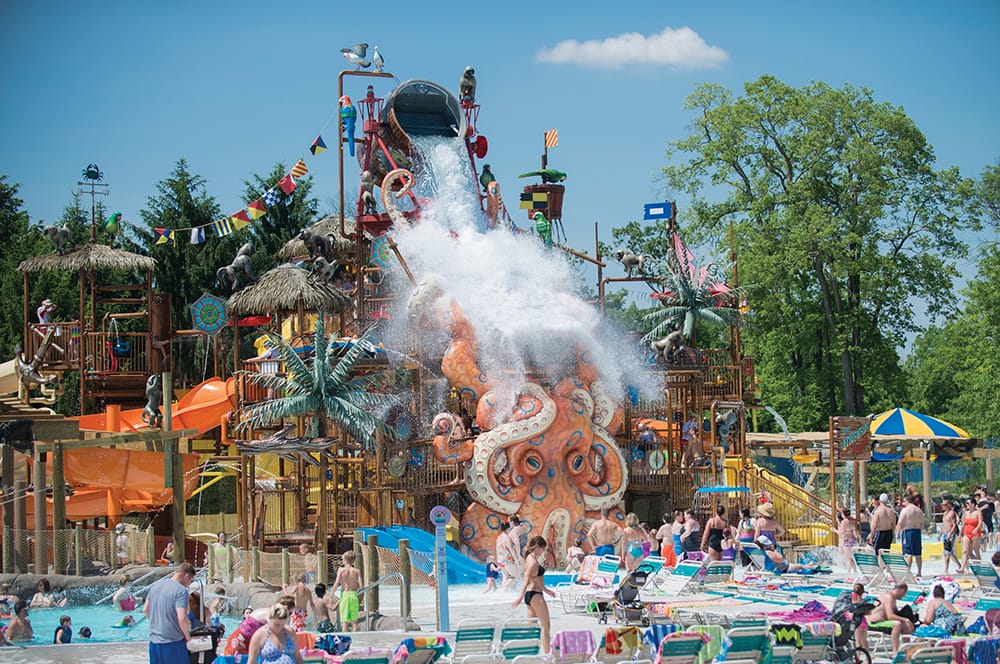
Checking Steel, Whether Galvanized Or Stainless
It’s good to know which parts use galvanized steel and which use stainless steel. Regularly inspecting steel supports for signs of damage and corrosion is good practice, including checking structural bolts weekly. If re-coating is necessary, the surface needs to be prepared beforehand, for example, with rust-inhibitive primers.
Bad practice is ignoring evidence of corrosion until it’s too late, leading to contamination, accidents, and major capital expenditures. Also, there is a 65- to 80-percent chance of coating failure when the surface is not adequately prepared.
Action: When checking the steel, also examine for environmental factors that influence corrosion rates; see if these can be adjusted, such as pH, stress, aeration, agitation, temperature, etc.
Keeping Capacity-Absorbing Play Structures Running
Aquatic play structures provide hours of interactive entertainment for a broad age range, as well as value for the money for water parks, so it’s essential to keep them running. Best practice is to perform daily, weekly, and end-of-season checks as required in the O&M manual as well as to ensure an inventory of spare parts.
Conversely, bad practice means ignoring signs of fatigue on the equipment and not having enough replacement on hand for the moving and high-wear parts, such as jets, nozzles, valves, and nets. This results in downtime or inefficient operations with high water and energy costs.
Action: Build in enough time and personnel to go through maintenance checks daily for the play structure. Don’t skimp on ordering enough spare parts.
OPERATIONS
Not Too Much, Not Too Little: Water Flow And Water Levels
Proper water levels and flow rate are crucial to the safe operation of a water slide. If the readings are incorrect, operators run the risk of riders traveling too fast or too slowly, potentially causing injuries.
Action: Check the water levels and flow using a flow meter daily.
Carrying Guests: Water Slide Vehicles
Ride vehicles, such as inner tubes, rafts, and mats, carry guests, so the vehicles must be in good condition and properly inflated as specified in the O&M manual. Torn or improperly inflated vehicles may result in a poor ride experience or even unsafe trajectory.
Action: Always make sure ride vehicles in service have not deteriorated and that attendants know what acceptable vehicle conditions look and feel like.
Supervision, Training, And Attitude
At successful water parks, every staff member feels empowered to take responsibility for safety and to report maintenance issues. They not only know what to do but why they do it. Unfortunately, there are facilities where staff members turn a blind eye to rules regarding the safe use and operation of equipment, fostering a “this is not my problem” attitude.
Action: Constantly train staff to be diligent about every aspect of safety, using up-to-date methods that are appealing to a respective age group, including in-person sessions, videos, or software/mobile apps. Make sure several staff members are experienced in maintenance procedures and that they are documented to avoid losing this knowledge when a key staff member departs.
Tip: Cross-train team members so they are able to help in different areas during low-staffing times.
Based in Vancouver, Canada, Chris Biancofiore is Director of Performance Services at WhiteWater, a designer and manufacturer of water parks. He has over 20 years of experience in the water-park industry, involving product development, manufacturing, and customer service. He currently serves as ASTM Subcommittee Co-Chair – Aquatic Play.